Understanding Key Mechanical Properties of Elastomers
The term “elastomer” is synonymous with “rubber”. Formally, elastomers are a special class of polymeric materials with unique properties such as elasticity, flexibility, and toughness. In today’s industrial landscape, we extensively use elastomeric materials for sealing. This is because elastomers are polymers that have high viscosity and elasticity, making them ideal for filling gaps and giving a tight, sealing fit.
Elastomer selection is mainly dependent on two criteria: mechanical properties, which are required to understand the structural characteristics of the elastomer, and chemical properties, which are used to understand what sort of chemicals the elastomer gives resistance to. Given below are some key mechanical properties needed to be understood when selecting your ideal elastomer:
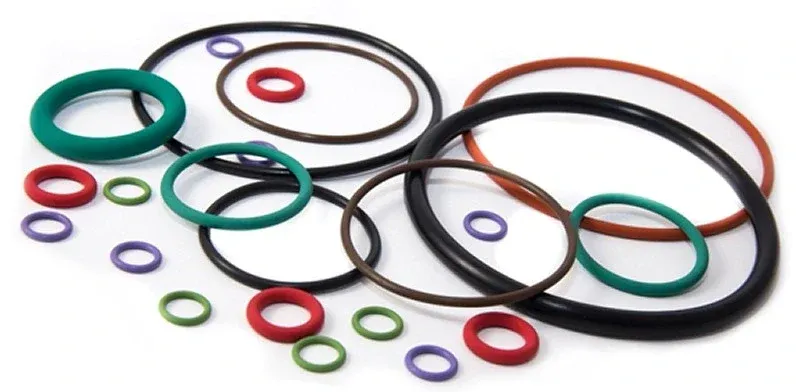
- Durometer Shore A: This is the hardness of an elastomer as measured by ASTM D2240. Hardness is measured on a scale of 0 (infinitely soft) to 100 (infinitely hard). The measurement is typically made on a pellet or layered sheets. This Shore A reading is an important indicator of how hard or soft your elastomer will be. For example, high pressure applications, or applications involving heavy water usually require harder elastomers. Also, the softer the elastomer, the better the seal material conforms to the surfaces to be sealed, hence being ideal for low pressure applications.
- Compression set: Rubbers deform under load and rarely return completely to their original form. The difference between the initial and final dimensions is known as compression set or permanent set. Compression set is tested as per ASTM D395. Dynamic packings need elastomers with lower compression sets. The compression set of an elastomer is always taken under specific test conditions. However, the compression set of different elastomers is likely to change with an increase in temperature.
- 100% Modulus: The value of “100% Modulus” is the stress recorded (measured in MPa) when the elastomer sample is stretched to double its original size. This test is performed per ASTM D412. Modulus tests are used for controlling product quality, and for determining the effect of chemical or thermal exposure on an elastomer/rubber.
- Elongation at Break %: This is the ultimate elongation of an elastomer at the point of its rupture. This test is performed per ASTM D412. Elongation at break is important in assessing a material’s capacity to plastically deform in a safe way, avoiding brittle failure. It is critical in applications for materials like elastomers where the material will be stretched repeatedly or subjected to impacts.
- Tensile Strength at Break: This is the stress recorded when an elastomer sample is stretched to its breaking point. This test is performed per ASTM D412. Tensile strength is an indication of how strong a compound is and is an important consideration specifically for applications where a large ‘pull’ force is present.
To find out more about the various mechanical properties of your elastomers, visit our website or contact our engineers today!